
Lunch for Bugs!!! The moths got to these old dampers. The numbers are my notations before disassembly. The darker dampers appear to be from the 1957 restoration. The '57 restoration was obviously quality work, but too much time has passed. The white dampers are obviously more recent--the craftsmanship on the more recent repairs is dismal.
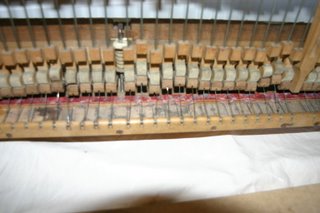
More filth here...that red felt on the bottom rail is almost entirely gone from moth damage.
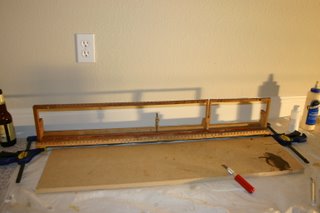
The damper frame completely stripped bare, with my beer in the corner.

New dampers going back in...
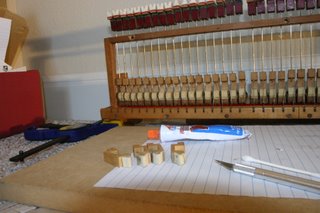
Making repairs to the sostenuto tabs where they meet the damper levers. There is no pin at the juncture, just a piece of buckskin glued on both pieces. This was a very time-consuming part of the operation.
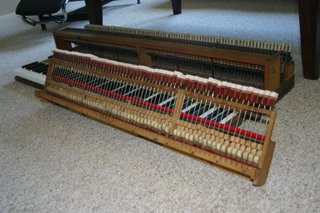
Here is the completed assembly, ready to be reinstalled.