Finished!
1859 Erard of Paris Grand Piano Restoration
This blog documents the restoration of my 1859 Erard grand piano. A note to Erard restorers: I am seeking to correspond with other Erard restorers and owners to share information on these instruments. Please contact me if you wish to start an online discussion group.
Monday, December 24, 2007
Thursday, September 27, 2007
Er, um, Actually it's 1858



Wednesday, July 25, 2007
Tuning Up!


Sunday, April 08, 2007
ReStringing
Mapes Piano Strings of Tennessee did these bass strings; the new strings are absolutely gorgeous and have wonderful tone. I am rapidly approaching completion...
Tuesday, March 06, 2007
Saturday, February 24, 2007
Finishing Soundboard Finishing
Saturday, February 17, 2007
Sealer Coat on the Soundboard
Finally! A few mist coats of sealer on the soundboard. I am using shellac from Rockler, with a 1.5 lb. cut. The blotchy parts along the left side will be hidden beneath the plate. I'll break down the spray kit, and brush from here on out...
Tuesday, February 06, 2007
Soundboard Restoration and Repair
Tuesday, January 09, 2007
Soundboard Preparation
Here is the plate removed from the case and sound board. I asked an experienced restorer over the internet about the procedure to get this out and he said..."you're a brave man for trying to remove the plate." Well, he was right, it sucked. Consider that every one of the 30 individual screws that I removed needs to be renovated and painted individually...

The pictures that follow show the plate removed, and some detail of what lurks underneath the slim aperture between the plate and the soundboard beneath. I do not believe that the plate has been removed for at least 80 years. The recent restorations were all done without removing the plate. Also, note that the instrument is no longer in the house, but in the workshop...
Wednesday, December 20, 2006
BARE!


Saturday, December 16, 2006
Destringing now, starting from the bass strings and moving up--it's a pain.
And here is the first test section I did with scrapers and a bit of sanding. This is too dusty to go further with in the living room, so I'll finish destringing and then move the piano into the garage for refinishing.
Wednesday, October 25, 2006
Miniaturization
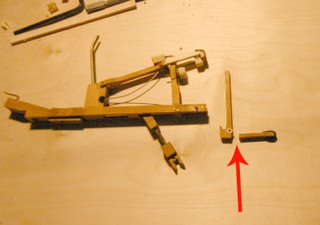
This photo shows a broken jack; the jack allows the hammer to "escape" from the piano key. Well, it's complicated, but without a jack when you press a key, the hammer just wacks against the string and stays there--"THUD"! I have two broken jacks--one came broken when I got it, and I broke one when I roughly removed the keys for refinishing.
Friday, September 08, 2006
Lyre Restoration
As you can see, these pictures show some stages of the restoration of the Lyre. Some interesting points: in the first picture, note the 3 brass bars. The one one the left I polished as a test. The two brass bars on the right were painted with a very poor brass paint. Why someone would paint brass with a poor imitation brass paint is lost on me. Perhaps they were so blackened with tarnish that they looked like steel--as I thought they were at first. In the 2nd and 3rd photos, you can see that I had to replace some decorative wood pieces that were lost to time. I did these with hand tools--a miter box, jigsaw, and hand drill. Man, do I need some better shop tools. Anyway, I am pleased with the results, all the brass is completely restored and polished, and lacquered, so it will not tarnish. Look at that brass shine, baby!
Friday, September 01, 2006
Three Legs!!!
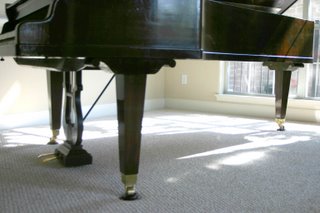
Finally, all three legs are complete: the veneering, finishing, and metalwork. When I spray the case I'll give the legs one more coat of finish...
Tuesday, August 15, 2006
Damper Restoration

Lunch for Bugs!!! The moths got to these old dampers. The numbers are my notations before disassembly. The darker dampers appear to be from the 1957 restoration. The '57 restoration was obviously quality work, but too much time has passed. The white dampers are obviously more recent--the craftsmanship on the more recent repairs is dismal.
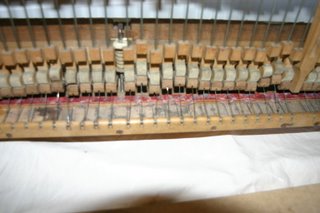
More filth here...that red felt on the bottom rail is almost entirely gone from moth damage.
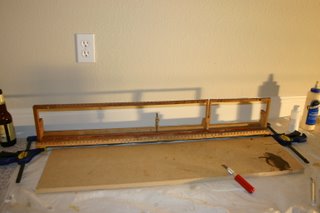
The damper frame completely stripped bare, with my beer in the corner.

New dampers going back in...
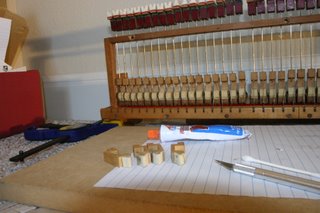
Making repairs to the sostenuto tabs where they meet the damper levers. There is no pin at the juncture, just a piece of buckskin glued on both pieces. This was a very time-consuming part of the operation.
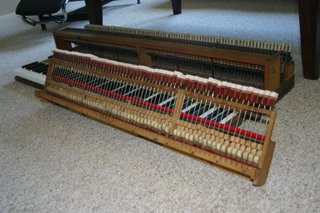
Here is the completed assembly, ready to be reinstalled.
Monday, August 07, 2006
Veneer Repairs on Legs

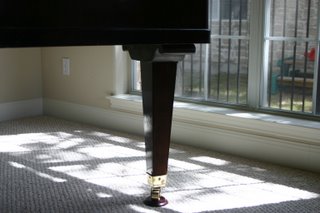
Here it is finished, with the new caster, and the ferrule polished like glass. The finish is minwax red mohogany and Jacobean colors layered until very dark, and 6 coats of polyurethane.
Voila!
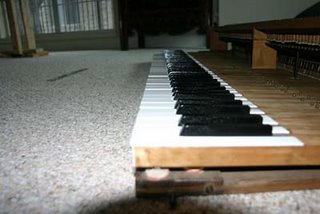
Friday, August 04, 2006
Piano Leg Restoration
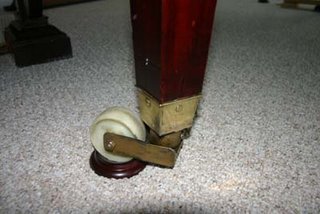
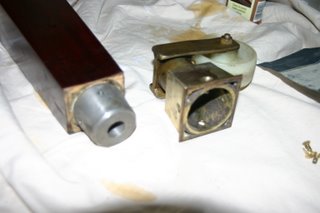
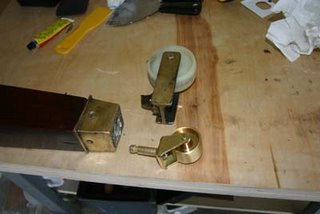
Here is the ferrule detached from the caster, and the new caster that will go into the leg. The bummer of this job is that it's noisy, messy, and I have to do it two more times for the two other legs.
Sunday, July 30, 2006

Message from 1957
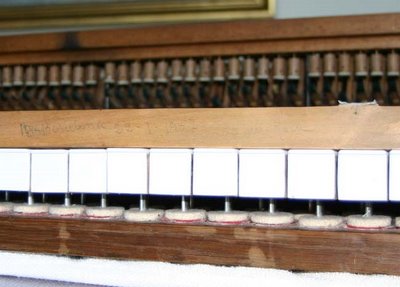

Subscribe to:
Posts (Atom)